Podejście DDMRP ma na celu zmniejszenie nadwyżek i niedoborów zapasów w łańcuchu dostaw produkcyjnych. Ogólnym celem planowania zapotrzebowania materiałowego na podstawie popytu jest przezwyciężenie trudności i niedociągnięć tradycyjnych metod planowania nowoczesnych, złożonych łańcuchów dostaw.
Podejście DDMRP różni się od tradycyjnego planowania zapotrzebowania materiałowego (MRP 1) i planowania produkcji na magazyn (MTS), ponieważ w mniejszym stopniu polega na prognozach. Pomaga również rozwiązać problemy w postaci długiego czasu realizacji charakterystycznego dla planowania produkcji na zamówienie (MTO), a także określa punkty rozmieszczenia strategicznych buforów zapasów oraz ich poziom.
Bufory zapasów używane w planowaniu zapotrzebowania materiałowego na podstawie popytu są również określane mianem „punktów rozłączenia”. Wynika to z tego, że każdy bufor zapasów pomaga rozłączyć sekwencyjne czasy realizacji, które w przeciwnym razie kumulowałyby się i wydłużały czas dostawy produktu do niedopuszczalnych poziomów. Jeśli na przykład bufor zapasów zostanie utworzony między między pośrednim, złożonym komponentem i etapem montażu komponentu w gotowym produkcie, czas dostawy produktu gotowego zostanie rozłączony od czasu realizacji tego złożonego komponentu.
Skrócenie czasu realizacji dzięki planowaniu zapotrzebowania materiałowego na podstawie popytu pomaga złagodzić jedną z większych bolączek produkcji na zamówienie i innych operacji typu ssącego. Ponieważ zamówienia sprzedaży uruchamiają konwencjonalne procesy MTO, wszystkie procesy produkcji są realizowane między momentem złożenia zamówienia i terminem dostawy. Efektywne przeniesienie części tych procesów do okresu przed otrzymaniem zamówienia pozwala skrócić czas realizacji zamówienia.
Planowanie zapotrzebowania materiałowego na podstawie popytu wykorzystuje niektóre aspekty podejścia MRP 1, łącząc je z elementami innych praktyk produkcyjnych. Jednym z takich elementów jest zastosowanie metod produkcji odchudzona (lean) do działań typu ssącego w celu ograniczenia kolejek oraz położenie nacisku na redukcję zmienności dzięki zastosowaniu metod Six Sigma w produkcji.
Powiązane produkty: Opcenter Advanced Planning and Scheduling
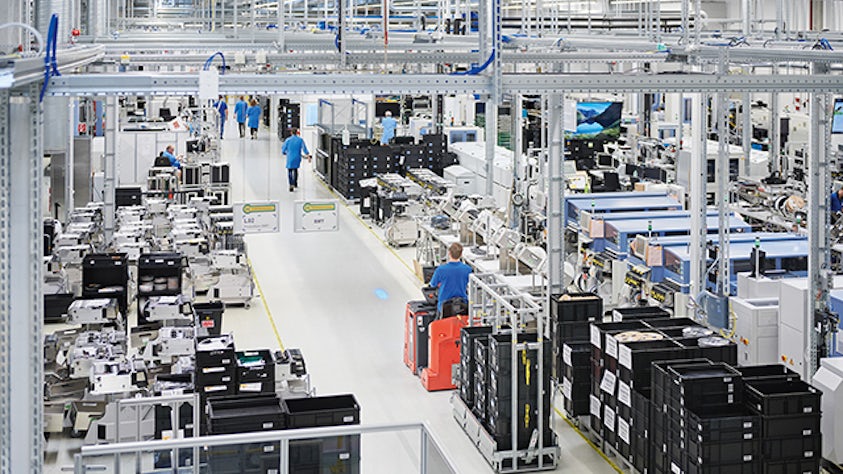