1980년대에 모토로라 엔지니어인 빌 스미스(Bill Smith)가 만든 식스 시그마라는 이름은 표준 편차(일반적으로 그리스 문자 시그마 σ로 표시)에서 유래합니다. 식스 시그마 이니셔티브의 목표는 결함 발생률을 백만분의 일 수준으로 줄이는 것입니다.
제조 식스 시그마는 린(Lean) 제조와 밀접한 관련이 있는 경우가 많습니다. 린 제조와 식스 시그마 이니셔티브는 모두 제조 결함과 낭비를 해소하여 품질과 효율을 개선하고자 합니다.
식스 시그마 제조 접근 방식은 린 제조 접근 방식과 다릅니다. 린 제조는 5단계 프로세스를 사용하여 다음과 같이 지속적으로 개선합니다.
- 가치 식별
- 가치 흐름 맵 구축
- 프로세스 흐름 생성
- '끌어오기' 설정(주문형 프로세스 생성)
- 지속적인 개선 및 완벽성
제조 식스 시그마는 변동을 해소하는 데 중점을 두어 비용을 절감하고 고객 만족도를 높입니다. 식스 시그마는 고객 경험에 기반하여 시작하고 데이터 기반 방식으로 실행됩니다.
관련 제품: Opcenter Execution | Opcenter Quality | Teamcenter Quality and Compliance Management
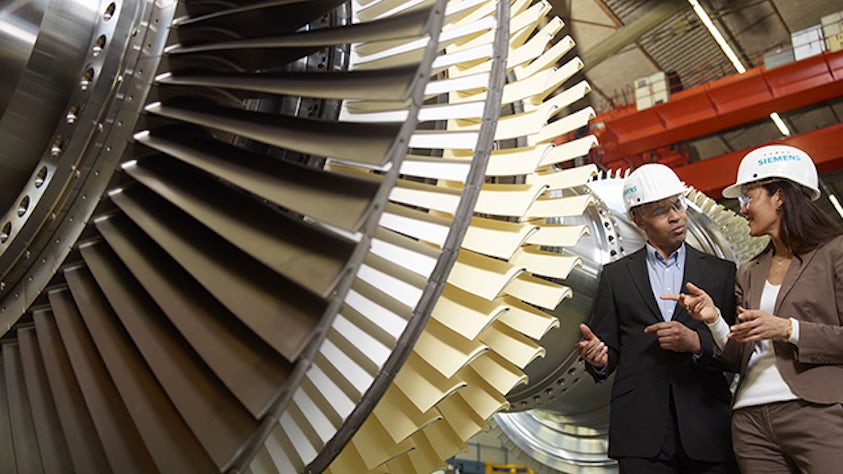