주문 생산은 생산 활동을 시작하는 이벤트(고객 주문)가 주문 이행으로 시작되며 생산 시퀀스를 통해 역방향으로 작동하여 계획 또는 일정에 도달하므로 풀(pull) 유형의 작업으로 분류됩니다. 즉, 생산은 수요에 의해 '주도'됩니다. 반면, MTS(재고 생산)는 푸쉬(push) 유형의 작업입니다.
주문 생산 계획은 소량 다품종 생산을 대량 생산의 효율로 실현하는 '대량 맞춤화' 시장 트렌드와 부합하므로 점차 확산되고 있습니다. 풀 작업에 속하는 주문 생산은 맞춤형 기능을 생산 실행에 통합합니다. 또한 주문 생산은 종종 낭비를 초래하는 과도한 재고를 최소화할 수 있습니다. 따라서 주문 생산은 린(Lean) 제조 및 JIT(적시) 스케줄링의 구성 요소인 경우가 많습니다.
주문 생산 계획에서는 주문을 받은 후에만 생산 주기가 시작되기는 하지만 리드 타임을 최소화해야 하는 과제를 해결해야 합니다. 이는 주문 생산이 생산 주기가 비교적 짧은 제품에 더 적합함을 의미합니다. 제조업체는 리드 타임을 줄이기 위해 자체적으로 상당한 리드 타임이 필요한 중간 제품 컴포넌트에 대해 재고 생산 방식을 채택하여 주문을 받은 후 이러한 중간 컴포넌트를 사용하는 프로세스 단계를 보다 빨리 시작할 수 있습니다. 이것이 DDMRP(수요 기반 재료 요구사항 계획)의 기본 개념입니다.
최신 APS(고급 계획 및 스케줄링) 시스템의 일부 기능은 주문 생산 계획을 최적화하도록 설계되었습니다. 계획 담당자가 APS 소프트웨어를 사용하면 수량 또는 납기 변경과 제조 용량의 변경 사항을 신속하게 평가하고 새로운 요구사항에 맞게 주문 생산 계획을 조정할 수 있습니다.
관련 제품: Opcenter APS
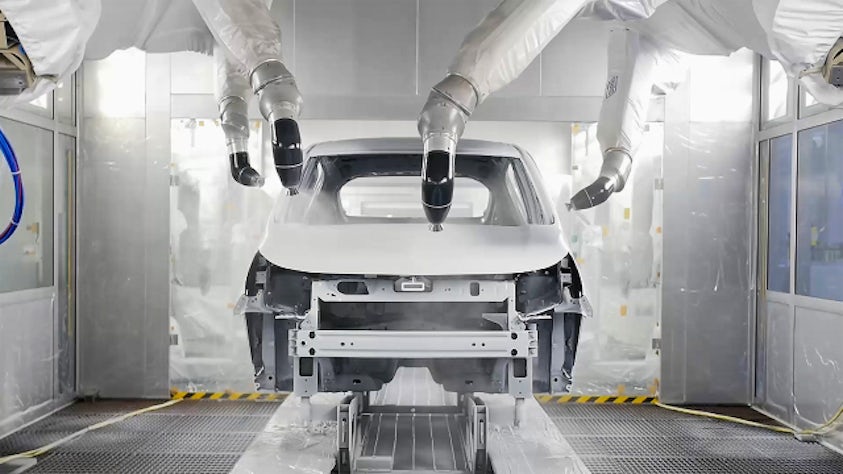