제조 및 어셈블리를 고려한 설계는 제품 라이프사이클의 초기 설계 단계에서 제품 부품의 제조 용이성과 최종 제품으로의 단순화된 어셈블리를 우선시하여 출시를 앞당기고 총 생산 비용을 줄이는 데 중점을 두는 엔지니어링 방법론입니다.
오늘날 하나의 철학으로 알려지기 전에, DFMA는 DFM(제조를 고려한 설계)과 DFA(어셈블리를 고려한 설계)라는 두 가지 별개의 방법론으로 간주되었습니다. DFMA는 문제를 해결하기에 가장 방해가 적고 비용이 적게 드는 시기인 제품 설계 단계에서 비용 효율적인 원자재를 선택하고 제조 작업의 복잡성을 최소화하여 제품 컴포넌트의 전체 제조 시간과 비용을 줄이는 데 중점을 둡니다. 마찬가지로, DFA는 개별 부품 수, 어셈블리 단계 및 제작 품질의 변동성을 최소화하여 제품의 어셈블리 시간, 비용 및 복잡성을 줄이는 데 중점을 둡니다.
DFM에 대해 고려해야 할 중요한 핵심 요소는 다음과 같습니다.
계획
설계에 대해 제조 전문가와 상의합니다. 제조 비용을 낮추는 것은 설계 단계에서 가장 쉽습니다.
재료
가능한 경우 제조 규정을 준수하는 재료를 사용합니다. 이는 제조 프로세스 및 수단, 재료 관리 및 품질 관리를 결정합니다.
프로세스
비용 절감을 위해 제조 프로세스를 숙지합니다. 예를 들어, 3D 프린팅을 사용하면 여러 컴포넌트를 제조하는 대신 하나의 모놀리식 부품으로 설계할 수 있습니다.
표준
표준 부품 또는 컴포넌트를 사용합니다. 이를 통해 새로운 설계 비용을 줄이는 동시에 재고 관리를 개선하고 출시를 앞당길 수 있습니다.
관련 제품: Teamcenter 제조 프로세스 계획 및 데이터 관리 | 제조를 고려한 Solid Edge 설계
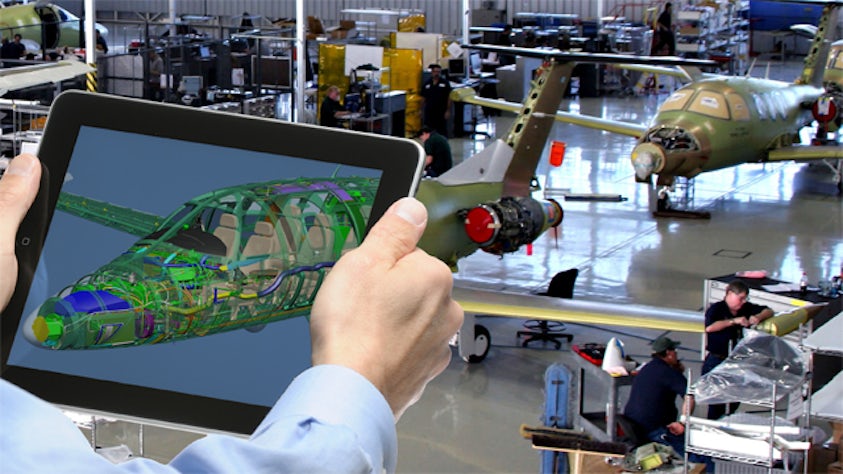