Les ressources de production peuvent inclure des matières premières, des composants provenant de fournisseurs, des équipements et du personnel de production, ou des pièces de rechange, c’est-à-dire toute ressource nécessaire à la production d’un produit fini. La planification des ressources de fabrication est abrégée en "MRP II" ou "MRP 2" pour la distinguer de la planification des besoins en matériaux (MRP I). La planification des ressources de fabrication 2 englobe toutes les capacités de la MRP I, qui se concentre sur l’inventaire des matières premières et des composants fournis par un fabricant. Le système MRP utilise ces données d'inventaire, ainsi que les commandes de production et les nomenclatures, pour calculer la quantité et établir le calendrier des achats de marchandises entrantes supplémentaires.
La planification des ressources de fabrication est gérée dans les systèmes modernes de gestion des opérations de fabrication (MOM) par un logiciel de planification et de programmation avancés (APS). Les logiciels de planification et de programmation avancés éliminent une grande partie de la saisie manuelle des données qui accompagnait les anciennes approches de planification des ressources de fabrication. Ce logiciel permet également au système MRP II de gérer des portefeuilles de produits très diversifiés dans le cadre d’exigences strictes de livraison aux clients, de scénarios complexes d’allocation des ressources et d’ordres de changement de dernière minute.
Le logiciel de planification des ressources de fabrication calcule et met à jour les besoins en matériaux en fonction des commandes réelles et des prévisions de commandes. La complexité des opérations de fabrication et de la planification a considérablement augmenté ces dernières années en raison de la complexité croissante des produits et de la chaîne d’approvisionnement, de la mondialisation, de la personnalisation de masse et d’autres facteurs. Par conséquent, le grand nombre de variables et de points de données à prendre en compte dans les logiciels de MRP a poussé de nombreux fabricants, même les petites et moyennes entreprises, à passer d’outils de MRP sur papier, tableurs et développés à des outils numériques intégrés tels que la planification et l’ordonnancement avancés.
La planification des ressources de fabrication repose sur le concept de « demande dépendante », qui fait référence au besoin d’une matière première ou d’un composant intermédiaire dépendant de la demande du produit fini. Un fabricant prévoit la demande pour un produit fini particulier, considérée comme une « demande indépendante » car elle provient d’une source externe, généralement le client ou une commande sur stock, et le logiciel de MRP calcule la demande de matériaux en fonction de cette prévision.
Aujourd’hui, l’objectif de la planification des ressources de fabrication est souvent lié aux méthodologies de planification juste-à-temps (JIT) et juste-en-séquence (JIS), qui visent à minimiser à la fois les niveaux de stock et la durée pendant laquelle un matériau reste stocké ou stationné à proximité de l’équipement de traitement qui l’utilisera. Ces stratégies doivent également garantir une quantité suffisante de stocks pour éviter toute pénurie ou tout arrêt de production.
Les résultats des logiciels de planification des ressources de fabrication répondent aux questions relatives à l’acquisition, au stockage et au déploiement, notamment :
- Quand commander chaque matériau
- En quelle quantité
- Auprès de quel fournisseur passer chaque commande
- Où conserver les stocks
- Quand déplacer le matériau (et en quelle quantité) du stockage à la ligne de production
La planification des ressources de fabrication peut également être utilisée pour s’adapter aux variations de l’offre ou de la demande. Par exemple, les informations concernant l’impact d’une catastrophe naturelle sur un fournisseur peuvent être prises en compte dans le système de planification des ressources de fabrication afin qu’un approvisionnement adéquat soit disponible en cas de besoin.
Produits connexes : Opcenter Advanced Planning and Scheduling
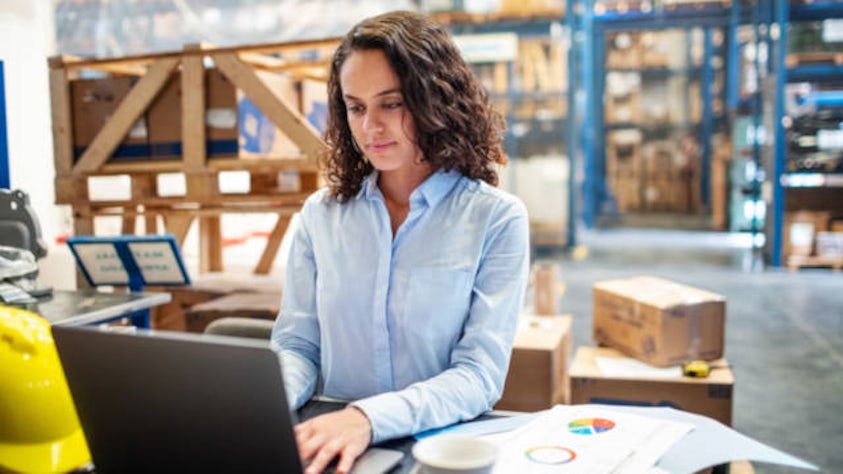