La DDMRP se ha diseñado para reducir el exceso de stocks y la escasez en la cadena de suministro de fabricación. El objetivo general de la planificación de requisitos de material según la demanda es superar las dificultades y deficiencias de los enfoques convencionales de planificación de las modernas y complejas cadenas de suministro.
La DDMRP difiere de la tradicional planificación de requisitos de material (MRP 1) y de la planificación de la fabricación para stock (MTS) porque se basa menos en las previsiones. También ayuda a superar el reto de los largos plazos de entrega asociados a la planificación de la fabricación para pedido (MTO). La DDMRP determina el punto de la cadena de suministro en el que colocar el inventario estratégico y cuál debe ser su tamaño.
Los inventarios utilizados en la planificación de requisitos de material según la demanda también se denominan puntos de desvinculación. Eso se debe a que cada serie de stocks ayuda a desconectar los plazos de entrega secuenciales que, de otro modo, se acumularían y alargarían el plazo de entrega hasta límites inaceptables. Por ejemplo, si se crea un inventario entre un componente intermedio y complejo y la etapa de ensamble que incorpora ese componente al producto acabado, el plazo de entrega del producto acabado se desvincula del plazo de entrega del componente complejo.
Los plazos de entrega reducidos que ofrece la planificación de requisitos de material según la demanda ayudan a mitigar uno de los inconvenientes destacados de fabricación para pedido y otras operaciones de «arrastre». Dado que los pedidos de venta activan convencionales operaciones de fabricación para pedido, todas las operaciones de producción tienen lugar entre el momento del pedido y el de la entrega. Al trasladar de manera eficiente algunas operaciones de producción al período anterior a la recepción del pedido, la DDMRP reduce el plazo de entrega.
La planificación de requisitos de material según la demanda se basa en algunos aspectos de MRP 1 y los combina con elementos de otras prácticas de producción. En concreto, la DDMRP emplea un método de «arrastre» de fabricación optimizada para limitar las colas en cada operación y se centra en la reducción de la variabilidad de Six Sigma en fabricación.
Productos relacionados: Opcenter Advanced Planning and Scheduling
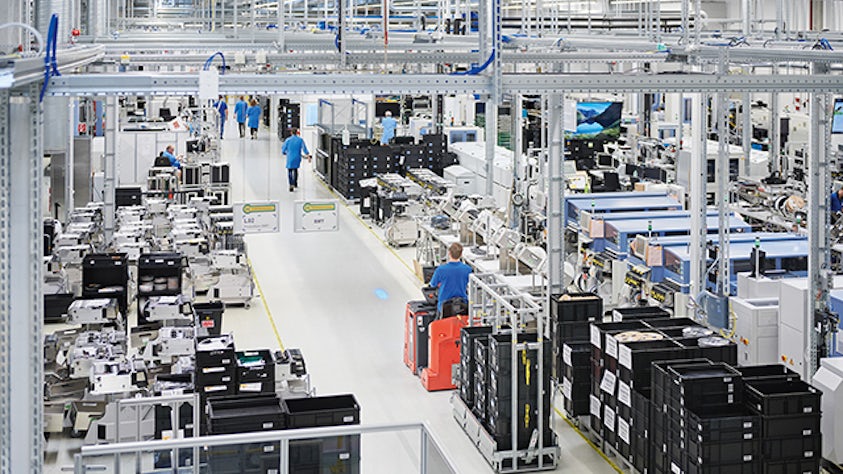