Vat photopolymerization is a category of additive manufacturing (AM) processes that create 3D objects by selectively curing liquid resin through targeted light-activated polymerization. Stereolithography, the first AM process to be patented and commercialized, is a vat photopolymerization technique. Since the advent of stereolithography in the 1980s, vat photopolymerization has grown to also include continuous liquid interface production (CLIP), solid ground curing (SGC), and direct light processing (DLP).
All types of vat photopolymerization use special resins called photopolymers as the printing material. When exposed to certain wavelengths of light, the liquid photopolymers' molecules rapidly bind together and cure into a solid state through a process called photopolymerization. In most 3D printers that operate under the principles of vat photopolymerization, liquid photopolymer is held in a container or vat with the build platform partially submerged near the surface of the liquid. Using the information supplied by a CAD file, the printer directs a light source to cure the liquid photopolymer into a solid layer selectively. Then, the build platform is re-submerged into the remaining resin, and the process is repeated for subsequent layers until the design has been fully printed.
Vat photopolymerization is known among manufacturers as a fast and very accurate AM process that can print large models and prototypes (with an appropriately sized vat and build platform). However, photopolymers generally do not have robust structural characteristics, so the resulting parts are inherently more prone to degradation and deformation over time. Additionally, printed parts may require special handling or additional tooling depending on the process and polymers used - making vat photopolymerization prohibitively expensive for some applications.
Related products: NX AM Fixed Plane | NX AM Multi-axis | NX AM Build Optimizer
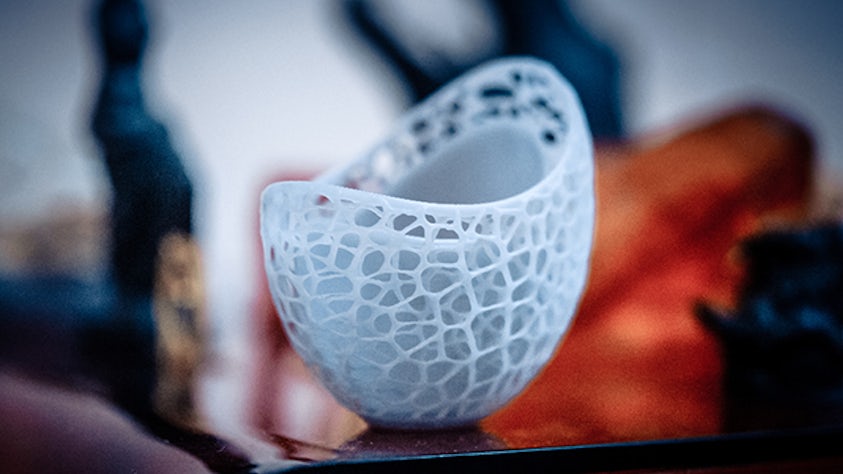