Service asset management (SAM) is a critical system within a service lifecycle management (SLM) solution, which in turn supports comprehensive product lifecycle management (PLM).
Service asset management software serves as a data source that comprehensively describes physical assets from their approved configurations to their operational state. This asset and service knowledge ensures an accurate configuration management core that enables all other service lifecycle management systems to be asset and product configuration-driven. Service and product teams use service asset management to access, view, and leverage a secure and single integrated source of information. Also called physical asset management, service asset management maintains the true configuration and performance data for an operational asset, and its underlying systems, subsystems, and components. Service teams use service asset management software to determine what parts can be used to resolve a service event as quickly as possible. They also use service asset management to evaluate the impacts of the proposed product or service-driven changes; they can assess the full impact of these changes on operational characteristics. Results of service activities are captured through service asset management to feed a closed-loop system that enables continuous product and service improvement.
Related products: Teamcenter
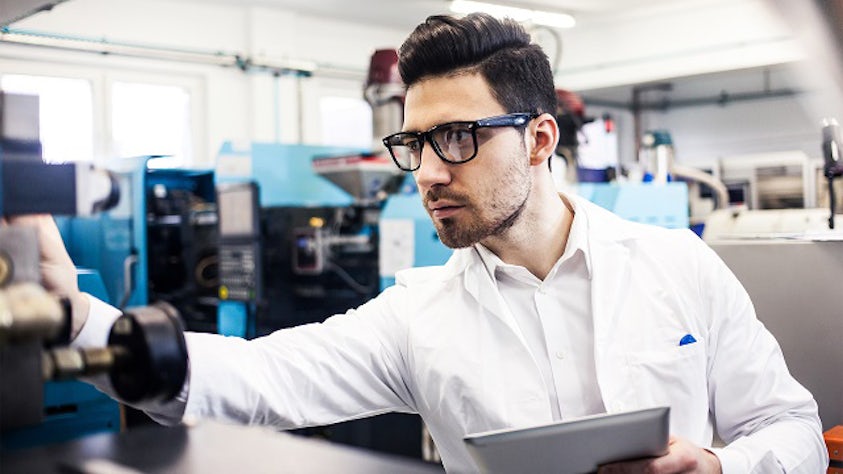