Reverse engineering is the process of analyzing a product, device or system to understand its design, construction or functionality. It involves disassembling, examining and studying the components and structure of an existing object to create a detailed representation or model of it. The primary goal of reverse engineering is to extract useful information or knowledge about how something works or is constructed without access to its original design documentation or specifications.
- Product development: To understand competitor products or improve existing designs.
- Manufacturing: To recreate obsolete or legacy parts, improve manufacturing processes or troubleshoot production issues.
- Software: To analyze and understand software code, create interoperable software components or develop patches for security vulnerabilities.
- Security: To identify vulnerabilities or weaknesses in hardware or software systems for cybersecurity purposes.
- Forensics: To analyze and reconstruct accidents, failures or incidents involving mechanical or electronic systems.
Key steps involved in reverse engineering
- Obtaining the object
The first step in reverse engineering is acquiring the object or product that needs to be analyzed. This could be a physical device, a mechanical component, an electronic circuit, a software code, or any other tangible or intangible item.
- Disassembly or deconstruction
Reverse engineers disassemble the object, either physically or virtually, to access its individual components and internal structure. This may involve taking apart mechanical parts, opening up electronic devices, or examining software code.
- Analysis and documentation
Once the object is disassembled, reverse engineers analyze and document its various components, materials, dimensions, connections and functionalities. They may use tools such as calipers, microscopes, scanners or software programs to gather data and create detailed documentation.
- Understanding design and functionality
Reverse engineers seek to understand the design principles, engineering decisions and functionality of the object being analyzed. This involves studying how different components interact with each other and how they contribute to the overall operation of the system.
- Reconstruction or replication
Based on the information gathered during the analysis phase, reverse engineers may reconstruct or replicate the object using CAD software, 3D printing, circuit design tools or other manufacturing techniques. This allows them to create a replica or modified version of the original object.
Reverse engineering examples in product design
Competitors often use reverse engineering to find product strengths they can adapt, or weaknesses they can improve. Reverse engineering can also be used to find information that is lost or unavailable – such as when revising someone else’s work or tracking the work of a criminal. Reverse engineering is also useful for digitalizing physical models or prototypes into computer-aided design (CAD) files. Modern design software usually has reverse engineering functionality built-in to accomplish this.
How to reverse engineer a product design from a 3D scan
There are times when it is either necessary or beneficial to analyze an existing product or structure to create a similar product. Reverse engineering can solve problems, improve a current model or even analyze a competitor’s model to build a similar product. Reverse engineering in product design starts with a finished product and deconstructs that to better design a similar product.
Easy 3D scanning reverse engineering
A 3D scan to CAD workflow supports engineers in mastering the challenges of reverse engineering, like improving or recreating an already existing object for which no design documentation is available. After 3D scanning an object for reverse engineering, the file can be directly imported into the 3D CAD software using formats such as STL or OBJ.
However, it is important to note 3D scanners don’t output a ready-to-manufacture model but point cloud or polygon mesh data. As a result, the 3D scanned data must be further modeled in CAD software.
Siemens’ software allows you to bring scanned data in as facets, so there is no need to map surfaces, create solids, or do manual shape creations.
Scan to CAD
The 3D scan to CAD workflow is more than “just pressing a button” and the skills of highly qualified engineers are required for reverse engineering.
Continuous technology improvements minimize the manual work the design engineer needs to invest in to produce high-quality 3D CAD models used for traditional manufacturing or 3D printing. Today, the 3D CAD software that is used as part of a 3D scan to CAD workflow imports the scanned data as facets, so there's no need to map surfaces, create solids, or do any other manual shape creation.
3D scanning 3D mesh
3D scanners are equipped to scan objects of all shapes and sizes. Specialized sensors scan the object from multiple angles and convert the object into a 3D mesh.
There are several 3D scanning technologies:
- Structured light 3D scanning
- Laser triangulation 3D scanning
- Laser pulse 3D scanning
- Contact-based 3D scanning
- Photogrammetry
Quality control as part of the design process
Quality management should always be part of the design process. To meet the increasing demand for digitizing high-quality designs and CAD models, 3D scanning to CAD is critical for getting products to market faster and without flaws. As quality requirements and processes evolve to be more complex, modeling scanned parts becomes more of a challenge.
A 3D scan accurately represents the real object, including defects. As part of the 3D modeling process, the scanned part gets inspected, and a color deviation map can be generated to detect warps or missing pieces.
In addition, 3D CAD software for reverse engineering allows you to compare whether different scanned parts have the correct dimensions, or you can compare the adjustments of two similar machines to determine whether there are differences in the alignment to correct.
Related products: NX CAD
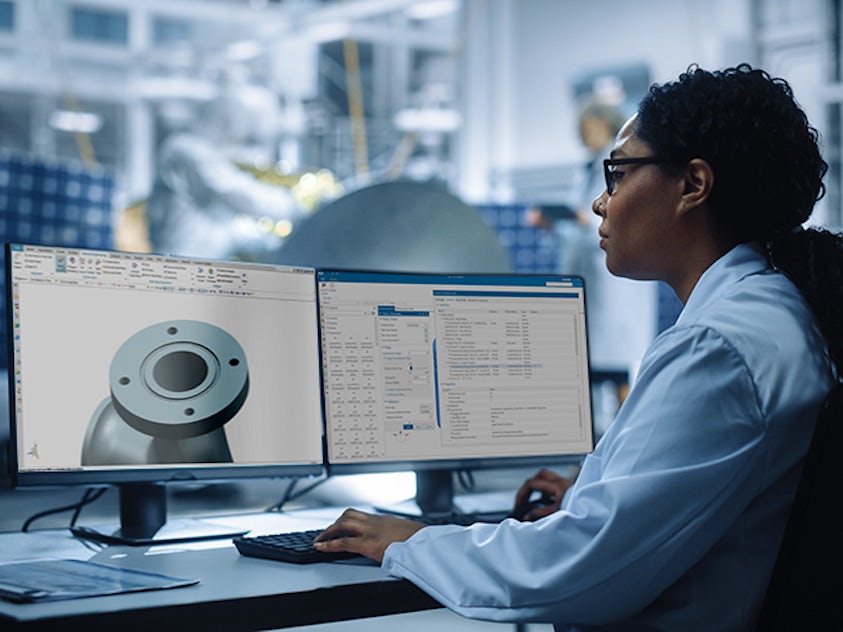