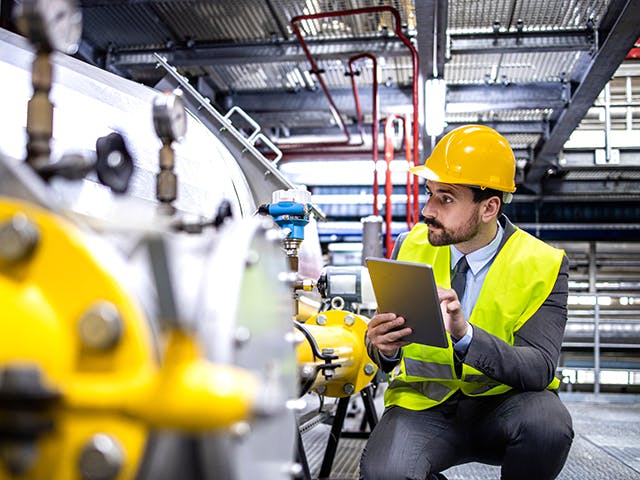
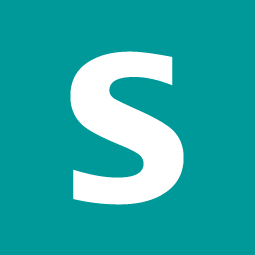
Quality standards are sets of good management practices to foster consistent production and product condition.
Quality standards are good management practices, methods, systems, requirements and specifications established by industry advisory groups to help manufacturers achieve and demonstrate consistent production and product quality. Some quality standards are applicable to a broad spectrum of manufacturing and service organizations, while others are industry specific.
Related products: Opcenter Quality | Teamcenter Quality and Compliance Management
As manufacturing companies pursue certification and then the maintenance of their quality management systems and practices, they almost always improve quality outcomes of their operations and may also increase efficiency and decrease costs.
Ensure that manufacturers understand and meet customer needs, continually improve processes, engage employees effectively, and make evidence-based decisions, ultimately delivering consistent and high-quality products
Standardize methods, processes, and documentation ensure compliance, fostering a safety-focused culture in product design and manufacturing.
Provide a structured framework that promotes consistency and conformity with industry regulations.
Establish standardized processes, thorough documentation, and a culture of continuous improvement, ensuring consistent product quality and regulatory adherence.
Foster international trust through adherence to recognized and standardized quality management principles.
Demonstrate commitment to high standards, ensuring consistent product quality, and meeting customer expectations, thereby fostering trust and preference in the market.
ISO 9000 and ISO 9001 – Published by the International Organization for Standardization (ISO), ISO 9000 is a family of standards and ISO 9001 is a standard within the ISO 9000 family, both setting out good management practices for quality management systems (QMS).
IATF 16949 – Developed by members of the International Automotive Task Force (IATF) and approved and published by ISO, IATF 16949 defines the requirements for quality management systems used by the automotive industry.
IAQG 9100—The International Aerospace Quality Group (IAQG) has laid out standards for quality management systems for aviation, space and defense organizations. Like IATF 16949, the IAQG 9100 standard is built upon the ISO 9001 standard, so compliance with the former entails compliance with the latter.
IRIS—The International Railway Industry Standard (IRIS) establishes a global system for evaluating quality outcomes from manufacturers that supply the railway industry.
FDA 21 CRF Part 11 – Commonly referred to as Part 11, this US Food and Drug Administration (FDA) standard applies to FDA-regulated industries, including pharmaceuticals, medical devices, diagnostics and biotech companies. It establishes requirements for manufacturing software system control, validation, auditing and documentation.
GMP/GLP – Good Manufacturing Practices (GMP) and Good Laboratory Practices (GLP) are regulations established by the US FDA for healthcare product manufacturers, especially those using laboratories and process manufacturing.
Generally, manufacturers design manufacturing quality standards to standardize methods, elements, QMS, auditing, certification, documentation and other systems. Manufacturers use these standards to ensure consistent quality across the industry and (often) across the globe.
Initially, concerns about significant consumer complaints prompted the development of some quality standards.
Manufacturing quality standards have evolved toward less flexible practices over specifications and directives. This approach leaves decisions in the hands of the individual manufacturing company to decide how best to implement the standard, given the particulars of their operation.
The ISO 9000:2015 standard, on which many quality standards are based, specifies seven quality management principles designed to guide companies toward improvement:
Quality Management Systems (QMS) can identify potential problems before quality issues occur when integrated effectively as part of a closed-loop quality process.