SIMATIC IT Preactor APS, now part of Opcenter, improves the synchronization of manufacturing processes through robust planning and scheduling tools. It enables increased resource utilization and on-time delivery, while also helping to reduce inventory levels and waste.
Enabling manufacturers to easily generate plans and schedules and then react quickly and intelligently to changes, Preactor APS software represents a pillar of Siemens’ manufacturing operations management (MOM) portfolio. Along with a manufacturing execution system (MES), quality management software (QMS), and manufacturing intelligence, SIMATIC IT Preactor APS makes up a holistic MOM solution that links enterprise software solutions with manufacturing floor automation.
Now under the Opcenter Advanced Planning and Scheduling umbrella, Preactor APS includes systems tailored to specific functional needs. SIMATIC IT Preactor Advanced Scheduling (AS) is used to schedule machines, production lines, resources, services, and logistics. Preactor AS is offered in multiple versions to meet the specific needs of each customer, including Preactor AS Standard, Professional, and Ultimate. SIMATIC IT Preactor Advanced Planning (AP) aids manufacturers in long- and mid-term planning for both make-to-stock and make-to-order operations. SIMATIC IT Preactor Express is free to use the edition of the Preactor family of production planning and scheduling solutions. All these systems are discussed in greater detail below.
Preactor APS software functionality
Preactor APS uses advanced math to analyze and calculate achievable production schedules, taking into account a range of constraints and business rules. This approach enables planners to generate and evaluate multiple scenarios. Without such powerful tools, manufacturers may use hours or even days to generate schedules using spreadsheets. These are difficult to maintain and if an unexpected change occurs, it is difficult to generate a new schedule. Preactor can be customized and configured as needed without disturbing core Preactor code. It can be used as a standalone system or integrated with enterprise and MOM software, including ERP, MES, data collection, forecasting, demand planning, and OEE applications. Key features of Preactor APS software include:
- BOM-level planning—The planning bill of materials (BOM) can be exploded, and then the production plan for lower-level items is calculated in the same way.
- Order-based multi-constraint scheduling—Users can apply a ranking or weighting to orders. Scheduling is created based on resource availability, additional constraints and materials required for the order.
- Advanced constraint modeling—Rules about concurrent rule usage, advanced interoperation constraints and other advanced resource constraints can be modeled.
- Advanced material handling—Custom rules can be implemented to ensure that sub-assemblies and raw materials are consumed according to business rules. Material allocation is determined based on system filters and the ranking of data.
- Advanced schedule optimization—Additional rules enable the minimization of changeover times and other schedule-optimizing actions.
- Assembly process visualization—Material explorer generates a graphical view of material dependencies as well as plots of stock levels over time.
- Interactive schedule visualization—Once an initial master production schedule (MPS) has been created, data can be displayed as stock profile graphs and capacity usage graphs. The MPS can be changed by simply clicking and dragging a point on the stock or capacity graphs and the production of a particular item can be moved from one planning period to another. Any changes are reflected in all linked plot and grid windows.
Related products: Opcenter Advanced Planning & Scheduling
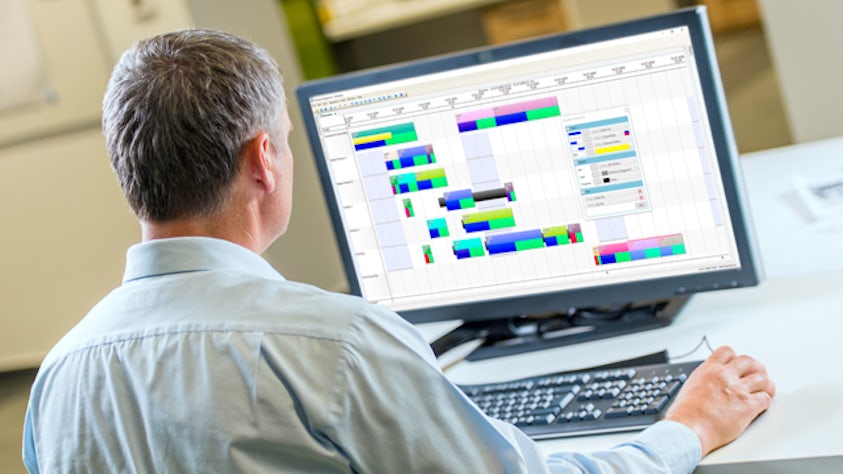