MRP I keeps track of a manufacturer's inventory of incoming raw materials and supplied components. The MRP system uses this information, along with production orders and bills of materials (BOMs), to calculate the quantity and timing of purchases of additional incoming goods. Material requirements planning is abbreviated "MRP I" (or "MRP 1") to distinguish it from manufacturing resource planning (MRP 2). MRP II encompasses all the capabilities of MRP I and optimizes other assets needed in a manufacturing operation: personnel, production equipment, spare parts and more.
When performed via a software solution, previous material requirements planning has involved a significant amount of manual entry and communication. In today's digitalized environments, MRP I software is supported by advanced planning and scheduling (APS) solutions, which utilize advanced algorithms to balance demand and capacity.
As product portfolios diversify under stringent customer delivery requirements, APS-enabled material requirements planning may help manufacturers meet demands with existing inventory or increase these resources prudently and with great efficiency. MRP I, when implemented through an effective advanced planning and scheduling solution, helps manufacturers meet global customer requirements such as lead time reduction, improved resource utilization, and accurate prediction of resource requirements. With APS-enabled MRP systems, manufacturers can compare different scheduling scenarios, improve productivity and track and control inventory.
Related products: Opcenter Planning | Opcenter Scheduling | Opcenter Scheduling SMT
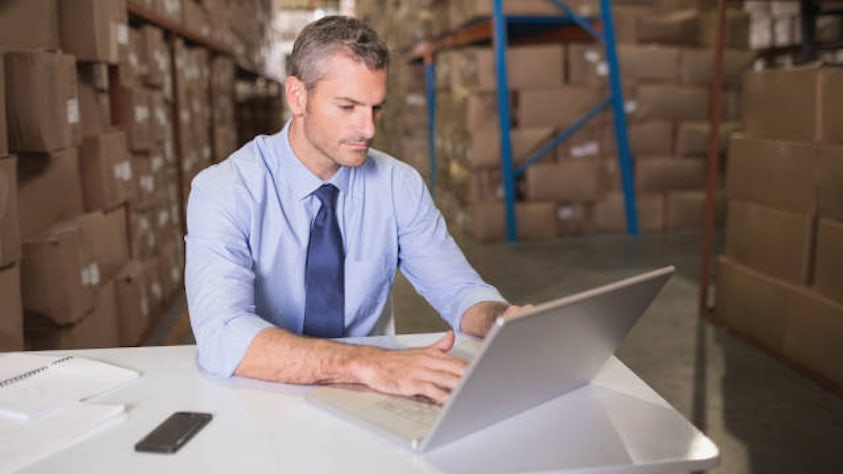