Production resources may include raw materials, components from suppliers, production equipment and personnel, or spare parts – any resource needed to complete the production of a finished good. Manufacturing resource planning is abbreviated "MRP II" (or "MRP 2") to distinguish it from material requirements planning (MRP I). Manufacturing resource planning 2 encompasses all the capabilities of MRP I, which focuses on a manufacturer's inventory of raw materials and supplied components. MRP I uses inventory data, production order and bill of materials (BOM) data to calculate the quantity and timing of purchases of additional incoming goods.
Manufacturing resource planning is handled in modern manufacturing operations management (MOM) systems by advanced planning and scheduling (APS) software. Advanced planning and scheduling software eliminates much of the manual data entry that has accompanied older approaches to manufacturing resource planning. It also enables the MRP II system to manage highly diverse product portfolios under stringent customer delivery requirements, complex resource allocation scenarios and last-minute change orders.
Manufacturing resource planning software calculates and updates material needs based on actual orders and order forecasts. The complexity of manufacturing operations and scheduling has increased dramatically in recent years due to growing product and supply-chain complexity, globalization, mass customization and other factors. As a result, the large numbers of variables and data points to consider in MRP software have caused many manufacturers – even small and mid-size businesses – to migrate from paper-based, spreadsheet and homegrown MRP tools to integrated digital tools such as advanced planning and scheduling.
Manufacturing resource planning relies on the concept of "dependent demand," which refers to the need for a raw material or intermediate component dependent upon the demand for the finished product. A manufacturer will forecast demand for a particular finished product – considered an “independent demand” because it arises from an external source, typically the customer or a make-to-stock order – and MRP software calculates the demand for materials based on this forecast.
The purpose of manufacturing resource planning today is often tied to just-in-time scheduling (JIT) and just-in-sequence (JIS) methodologies, which seek to minimize both inventory levels and the amount of time a material remains in storage or stationed near the processing equipment that will employ it. Such strategies must also ensure sufficient inventory is present to avoid any shortfalls or production stoppages.
The output of manufacturing resource planning software answers the questions about acquisition, storage and deployment, including:
- When to order each material
- How much to order
- With which supplier to place each order
- Where to store inventory
- When to move material (and how much) from storage to the production line
Manufacturing resource planning also can be used to accommodate changes in supply or demand. Information about the impact of a natural disaster on a supplier, for example, can be accounted for in the manufacturing resource planning system so that an adequate supply is available when needed.
Related products: Opcenter Advanced Planning and Scheduling
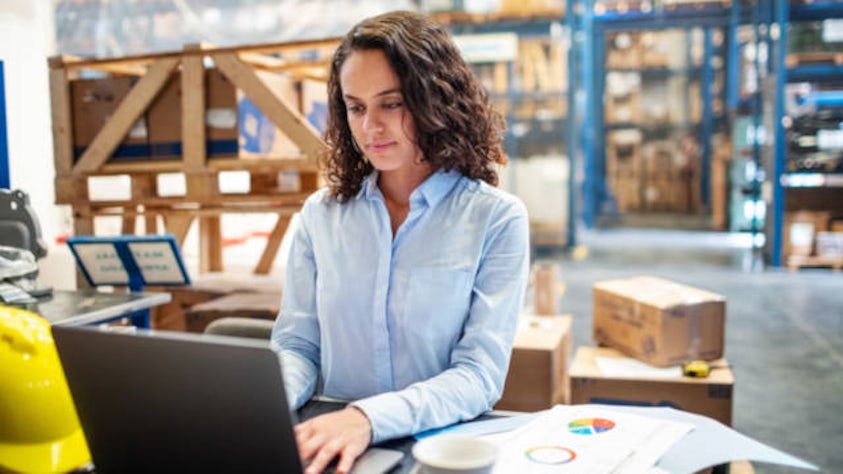