Manufacturing cost control encompasses the strategies and practices implemented to regulate and optimize production processes within a manufacturing environment. It revolves around managing resources effectively, including labor, materials, and equipment, to ensure that operations run smoothly while minimizing costs and maximizing output. This involves setting and monitoring production schedules, maintaining quality standards, and promptly addressing deviations or issues to prevent disruptions.
Manufacturing cost control involves using tools and systems to monitor real time performance, allowing for quick adjustments and informed decision-making. By integrating data from various sources and leveraging technology such as Enterprise Manufacturing Execution and Quality systems, companies can enhance visibility across the production chain, identify areas for improvement, and drive continuous optimization. Ultimately, effective manufacturing control is essential for achieving operational excellence, meeting customer demands, and maintaining competitiveness in today's dynamic market landscape.
Cost control in manufacturing
Cost control in manufacturing relies on timely and accurate work-in-process information integrated with corporate planning systems. This integration facilitates optimal business process interoperations and realistic production plans. When combined with lean manufacturing principles, this comprehensive planning and control approach ensures both cost control and superior customer service.
Related products: Opcenter Execution | Opcenter Quality
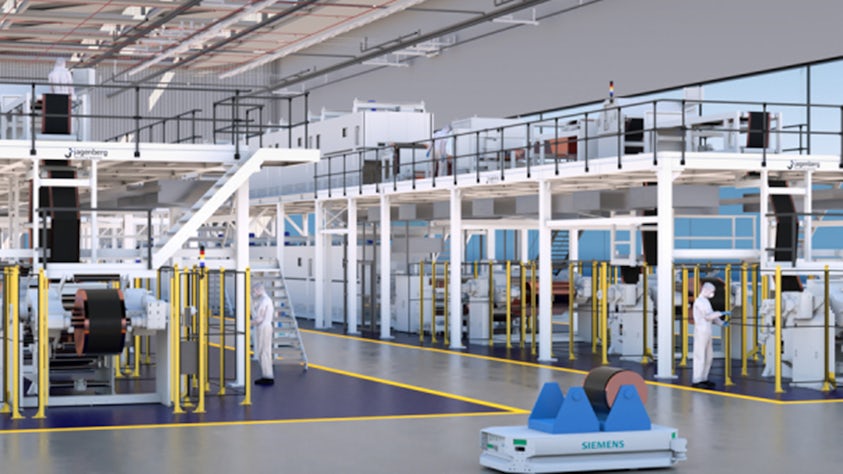