Products made during one production period are used to fulfill orders made in the next production period. This means that in make-to-stock production planning, production is triggered prior to and independent of specific customer orders.
Make-to-stock is considered a push-type operation, which means supplies – raw materials and supplier-provided components – are “pushed” through the production process, and planning starts with supplies and works forward to the finished product. In contrast, make-to-order (MTO) is a pull-type operation.
In today’s manufacturing marketplace, a high inventory of finished goods is usually an unacceptable cost burden, imposing the expenses of inventory management, warehousing, spoilage and more. Likewise, inventory shortages are costly because of expediting premiums, overtime, and missed delivery times. Therefore, the ideal of make-to-stock production planning is to match the quantity of finished goods at any given time with customer demand during the next period of time. To approach this ideal, planners must successfully forecast demand and appropriately balance supplies and production capacity to meet that demand.
Two keys to efficient make-to-stock planning are (1) accurate demand forecasting and (2) tools that enable rapid adjustments to changing forecasts. Demand forecasting has become more challenging in nearly every market because of the growing variety of products for which a manufacturer must forecast demand, as well as inherently unpredictable factors affecting demand – natural disasters, health crises, and certain seasonal variations (e.g., geopolitical or weather-related shortages of raw materials), to name a few.
Modern advanced planning and scheduling (APS) systems offer make-to-stock planners the digital tools needed to generate achievable, efficient plans and schedules and quickly adjust to changes in demand forecasts, supply availability, and production capacity. Advanced planning and scheduling software can also automatically make schedule adjustments based on real-time data.
Related products: Opcenter Advanced Planning and Scheduling
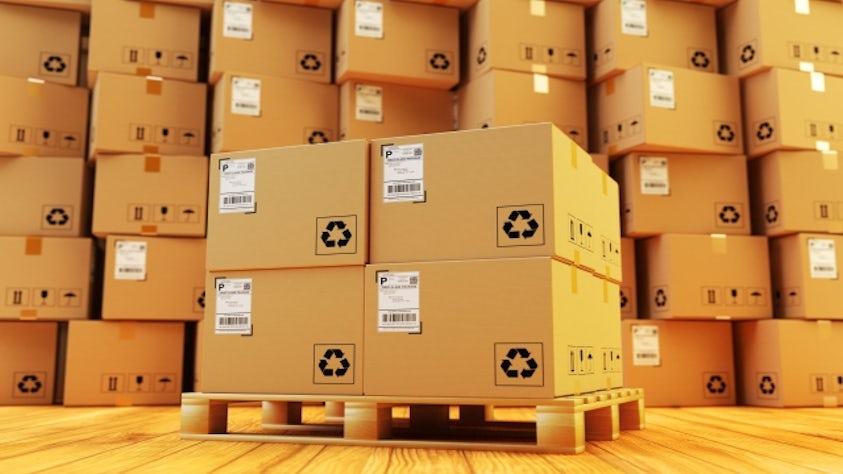