Make-to-order is considered a pull-type operation because the event that initiates production activity – the customer order – starts with order fulfillment and works backward through the production sequence to arrive at a plan or schedule. That is, production is “pulled” by demand. In contrast, make-to-stock (MTS) is a push-type operation.
Make-to-order planning is becoming more prevalent because it is compatible with the market trend of “mass customization,” which entails small batch or lot sizes manufactured at mass-production efficiencies. As a pull operation, make-to-order incorporates customized features into the production run. Make-to-order also helps to minimize excess inventory, which frequently results in waste. As such, make-to-order is often a component of lean manufacturing and just-in-time (JIT) scheduling.
A major challenge of make-to-order planning is to minimize lead time despite the fact that the production cycle commences only after the order is received. This means make-to-order is more amenable to products with relatively short production cycles. To reduce lead time, manufacturers may employ a make-to-stock approach for intermediate product components that require a significant lead time of their own so that process steps using such intermediate components can commence more quickly after an order is received. This is the concept behind demand-driven material requirements planning (DDMRP).
Some functionality in a modern advanced planning and scheduling (APS) system is designed to optimize make-to-order planning. APS software enables planners to quickly assess changes in quantity or delivery date, as well as changes in manufacturing capacity, and adjust the make-to-order plan to meet the new demands.
Related products: Opcenter APS
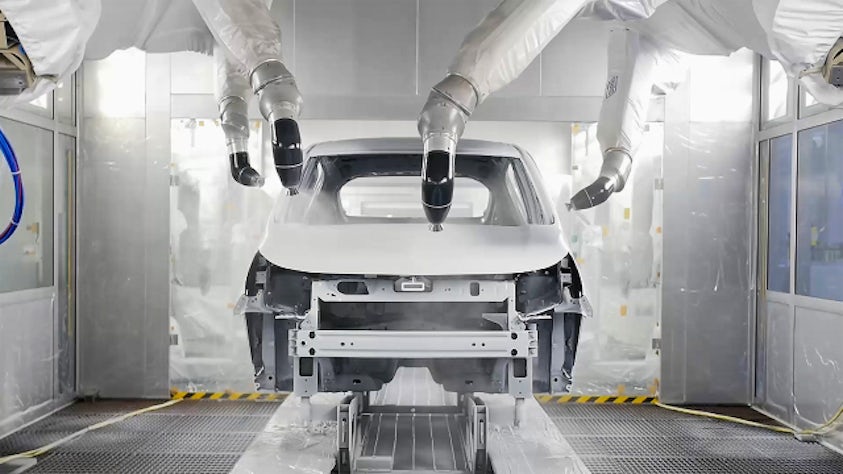