Just-in-time scheduling is one aspect of the general principle of just-in-time production. The primary goal of JIT production is to minimize the time between receiving supplies and delivering the finished product to the end customer. Although JIT production was conceived as a standalone methodology (about 50 years ago by the Toyota Motor Corporation), today it is typically considered one aspect of lean manufacturing.
Just-in-time scheduling is how a manufacturer ensures, on a day-to-day basis, that each order is produced with just enough time to achieve on-time delivery. This same objective characterizes just-in-time planning, but the time horizon for JIT planning is weeks or months. Just-in-time scheduling enables a manufacturer to adjust to last-minute changes, which may arise due to work order modifications, time overruns, material availability issues, and other factors. JIT scheduling is designed to avoid late deliveries on the one hand, and a backlog of materials, WIP and finished goods on the other.
By reducing backlogs and inventories, just-in-time scheduling helps companies reduce waste from expired or damaged materials. Manufacturers also cut costs associated with warehousing inventory or stockpiling materials along a production line. With just-in-time scheduling, production cycles can also be optimized so that companies enjoy greater productivity from their manufacturing facilities.
As with other manufacturing planning and scheduling tasks, the execution of just-in-time scheduling has evolved from a paper-based operation to an application of general spreadsheet programs to interactive software systems designed specifically for planning and scheduling. Today, advanced planning and scheduling (APS) systems manage the complexities of manufacturing schedules. APS systems accomplish just-in-time scheduling with powerful tools that account for the many factors that affect the production schedule:
- Availability of raw materials and other supplies
- Availability of production resources (equipment, personnel)
- Size and delivery date of each order
- Operating speed and capacity of each machine to be used on each order
- Production line changeover time
- New orders that require fast turnaround
Related products: Opcenter Advanced Planning and Scheduling
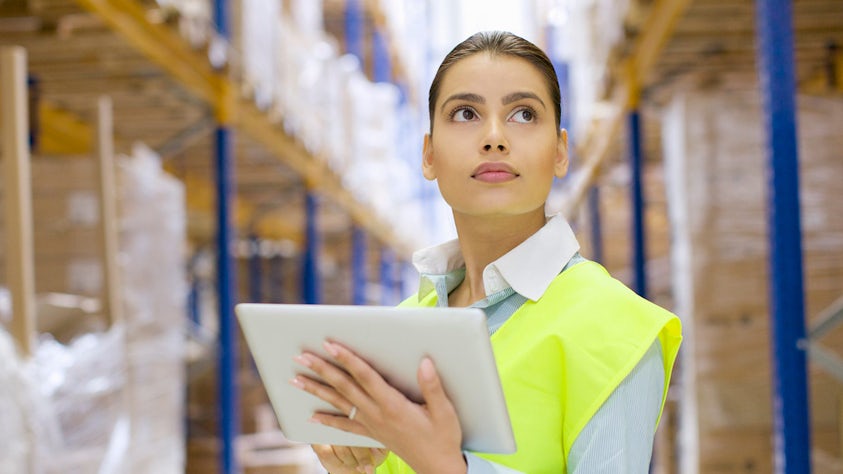