ISA-95 is the international standard for the integration of enterprise and control systems. ISA-95 consists of models and terminology. Its official name is “ANSI/ISA-95 Enterprise-Control System Integration” (known internationally as IEC/ISO 62264). However, the standard title does little to provide any information regarding its value. Leveraging this standard can bring a company-wide perspective to system integration that allows you to take thousands of actions and data points and boil them down in an understandable framework. It focuses on activities - and it is meant to define and integrate the activities between business and ERP on one hand and Manufacturing Execution Systems (MES) and Manufacturing Operations Management (MOM) on the other. The standard even covers the detailed level of sensors and the physical processes.
These models can be used to determine which information has to be exchanged between systems for sales, finance, and logistics, and systems for production, maintenance, and quality. This information is structured in UML models, which are the basis for the development of standard interfaces between ERP and MES systems. The ISA-95 standard can be used for several purposes, for example as a guide for the definition of user requirements, for the selection of MES suppliers, or as a basis for the development of MES systems and databases.
ISA-95 incorporates the layers model of technology and business processes for manufacturing enterprises as levels for the standard. These levels are:
Level 0 - Defines the actual physical processes.
Level 1 - Defines the activities involved in sensing and manipulating the physical processes.
Level 2 - Defines the activities of monitoring and controlling the physical processes.
Level 3 - Defines the activities of workflow to produce the desired end products.
Level 4 - Defines the business-related activities needed to manage a manufacturing operation.
Manufacturing Operations Management systems reside in Level 3 of the model. From a component or software perspective, Levels 1 to 4 can be seen like this:
Level 1: Intelligent devices
Level 2: Control systems (e.g., PLCs, DCSs)
Level 3: Manufacturing operations systems (e.g., MES)
Level 4: Business logistics systems (e.g., ERP)
Related products: Opcenter Intelligence, Opcenter Execution
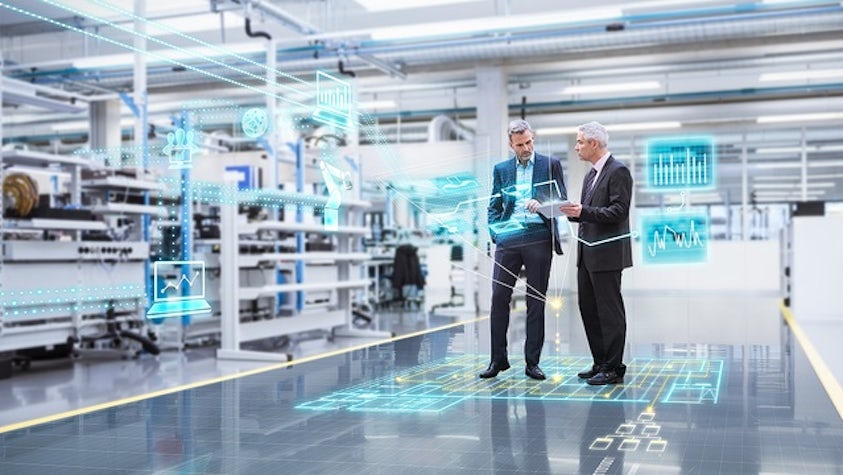