Failure Mode and Effects Analysis (FMEA) is an important technique in quality management for the manufacturing industry. It involves systematically identifying potential failure modes in products or processes and evaluating their impact on overall quality. By prioritizing these failures based on severity, occurrence and detectability, FMEA helps manufacturers address the most critical issues that could affect products and processes and meet customer satisfaction.
In manufacturing, FMEA is applied during both the design phase (Design FMEA) and the process phase (Process FMEA). Design FMEA aims to prevent failures by assessing risks in the product design before production starts, while Process FMEA focuses on identifying and mitigating risks in the manufacturing process itself. This proactive approach allows manufacturers to implement corrective and detective actions early, reducing the likelihood of defects and ensuring a smoother production flow.
FMEA software tools enhance this process by providing a structured framework for documenting and analyzing potential failures. These tools facilitate the organization of complex systems, enable efficient risk assessments and support the prioritization of corrective and detective actions. By integrating with other quality management systems, FMEA software ensures that all relevant information is accessible and up-to-date, helping manufacturers maintain high standards of quality and compliance.
Related products: Opcenter X Quality | Teamcenter Quality & Compliance
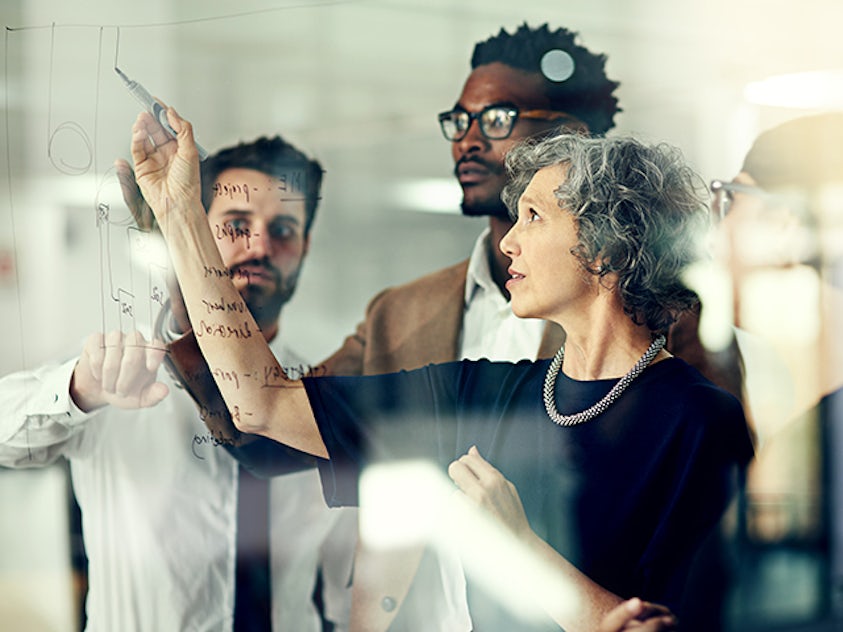