By leveraging automation tools and techniques, organizations can achieve greater efficiency, reduce errors and deliver high-quality engineering designs in less time.
Engineering automation refers to the use of software to automate repetitive engineering processes. With user-defined engineering rules and procedures, engineering automation tools are capable of creating data, schematics, documentation and more. This helps accelerate the development of products and allows engineers from different departments to work in parallel - leveraging innovative techniques that help designers meet demands for higher productivity machines, shorter design times and lower costs.
Related products: NX CAD | Simcenter 3D software
Engineering automation in CAD
Engineering automation in computer-aided design (CAD) refers to the process of using software tools and techniques to automate various aspects of the engineering design process. This automation aims to streamline repetitive tasks, improve efficiency, and enhance productivity in the design and engineering workflow. Key aspects of engineering automation in CAD include:
Parametric modeling:
Parametric modeling allows designers to define geometric features and relationships using parameters and constraints. Engineering automation enables the creation of parametric models that can be easily modified and updated, saving time and effort when iterating on design variations.
Design automation:
Design automation involves automating the creation of CAD models based on predefined rules, templates, or algorithms. This could include generating standard components, assemblies, or configurations based on user inputs or design specifications.
Customization and scripting:
CAD software often provides scripting or programming capabilities that allow users to automate repetitive tasks or customize workflows. Engineers can write scripts or macros to automate tasks such as geometry generation, data manipulation, or report generation.
Integration with engineering tools:
Engineering automation in CAD involves integrating CAD software with other engineering tools and systems, such as simulation, analysis, and data management software. This integration enables seamless data exchange and workflow automation between different stages of the design process.
Batch processing:
Engineering automation allows users to perform batch processing of CAD tasks, such as batch conversion of file formats, batch rendering of images, or batch updating of drawings. This can significantly reduce manual effort and improve productivity, especially for large-scale projects.
Standardization and templates:
Engineering automation promotes the use of standardized templates, libraries, and design guidelines to facilitate consistent and efficient design practices. Standardized components and templates can be reused across projects, reducing design time and ensuring consistency in design outputs.
Data-driven design:
Automation in CAD enables data-driven design processes, where design decisions are informed by data analytics, simulation results, or historical performance data. This approach allows engineers to optimize designs based on quantitative metrics and performance criteria.
Engineering automation integrated into PLM software
Engineering automation is often a key component of Product Lifecycle Management (PLM) software. PLM encompasses a set of software tools, processes, and methodologies that manage the entire lifecycle of a product from conception, through design and manufacturing, to service and disposal. Engineering automation within PLM software aims to streamline and automate various engineering tasks and processes across the product lifecycle.
Benefits of engineering automation in PLM software
Design automation:
PLM systems often include capabilities for automating design tasks such as parametric modeling, assembly generation and configuration management. Design automation tools allow engineers to create and modify CAD models more efficiently by leveraging predefined rules, templates and standard components.
Workflow automation:
PLM software facilitates the automation of engineering workflows and processes, such as change management, approval processes and document control. Workflow automation ensures that tasks are routed to the appropriate stakeholders, approvals are obtained efficiently and changes are managed effectively throughout the product lifecycle.
Integration with CAD and CAE tools:
PLM systems integrate with Computer-Aided Design (CAD) and Computer-Aided Engineering (CAE) software to automate data exchange and synchronization between design, analysis, and simulation tools. This integration enables seamless collaboration and ensures that design changes are propagated across all relevant systems and stakeholders.
Manufacturing automation:
PLM software includes capabilities for automating manufacturing processes, such as bill of materials (BOM) generation, routing optimization, and production scheduling. By automating these tasks, PLM systems help manufacturers improve efficiency, reduce errors and accelerate time-to-market.
Data management and integration:
PLM solutions provide centralized data management capabilities that enable automation of data-related tasks such as version control, data synchronization and data migration. Integration with enterprise systems such as Enterprise Resource Planning (ERP) and Customer Relationship Management (CRM) systems further automates data exchange and ensures data consistency across the organization.
Product documentation and reporting:
PLM software automates the generation of product documentation, including engineering drawings, specifications, manuals, and reports. By automating documentation tasks, PLM systems help ensure that accurate and up-to-date documentation is available throughout the product lifecycle.
Overall, engineering automation within PLM software plays a crucial role in improving efficiency, reducing errors and accelerating product development processes. By automating repetitive tasks and streamlining workflows, PLM systems help organizations achieve greater productivity and innovation while ensuring the quality and integrity of their products.
At Siemens, Teamcenter PLM and NX CAD do integrate engineering automation capabilities, which further enhances their functionalities and benefits for users across various stages of the product lifecycle.
The integration of engineering automation capabilities in Teamcenter and NX enhances productivity, collaboration and efficiency across the product lifecycle, from design and development to manufacturing and service. By streamlining workflows and automating repetitive tasks, users can focus more on innovation and value-added activities, leading to faster time-to-market and higher-quality products.
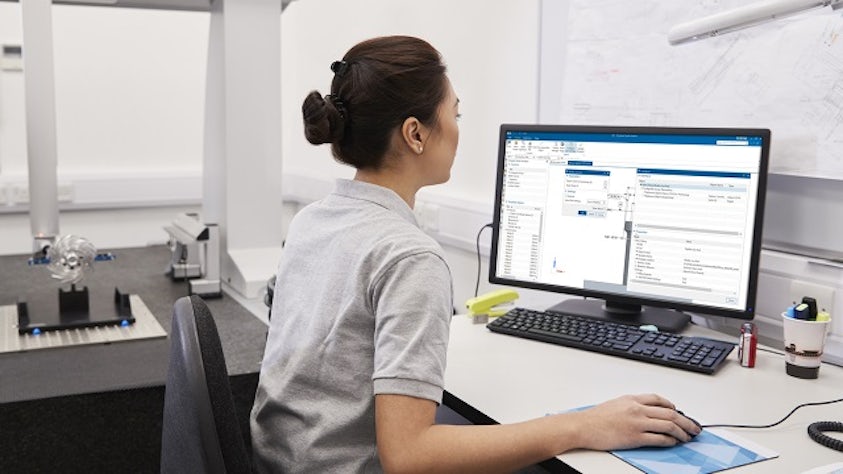