Design for manufacturing and assembly is an engineering methodology that focuses on reducing time-to-market and total production costs by prioritizing both the ease of manufacture for the product’s parts and the simplified assembly of those parts into the final product – all during the early design phases of the product lifecycle.
Before becoming the singular philosophy it's known as today, DFMA used to be considered as two distinct methodologies: Design for Manufacturing (DFM) and Design for Assembly (DFA). DFMA is concerned with selecting cost-effective raw materials and attempting to minimize the complexity of manufacturing operations during the product design phase (which would be the least disruptive and expensive time to address those issues) in order to reduce the overall manufacturing time and costs for the product components. Similarly, DFA is concerned with reducing the product's assembly time, costs and complexities by minimizing the number of individual parts, assembly steps and potential for variability in build quality.
Key factors that are important to consider for DFM:
Planning
Consult with manufacturing experts on your design. Lowering manufacturing costs is never easier than at the design stage.
Materials
Use manufacturing-compliant materials if possible, which determine manufacturing processes and means, materials management and quality control.
Processes
Know the manufacturing process to reduce costs. For example, 3D printing may enable one monolithic part design instead of manufacturing multiple components.
Standards
Use standard parts or components. This will reduce the cost of new designs while improving inventory management and time-to-market.
Related Products: Teamcenter Manufacturing process planning and data management | Solid Edge Design for Manufacturing
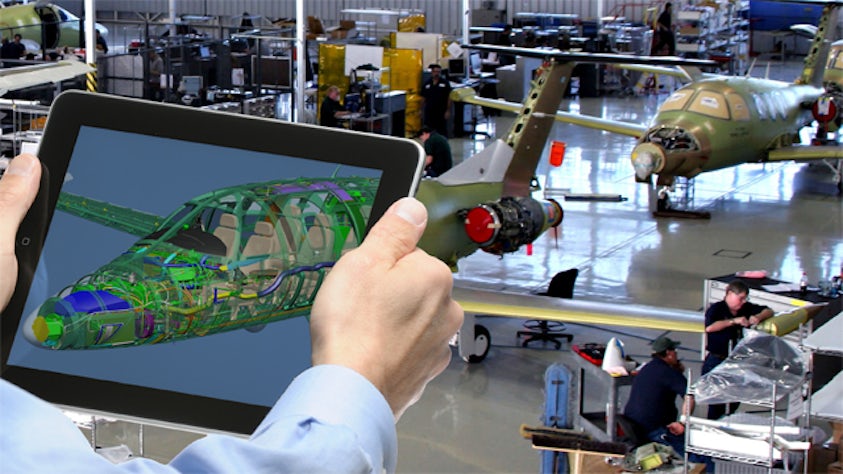