DDMRP is designed to reduce overstocks and shortages in the manufacturing supply chain. The overall purpose of demand-driven material requirements planning aims to overcome the difficulties and shortcomings of conventional planning approaches to modern, complex supply chains.
DDMRP diverges from traditional material requirements planning (MRP 1) and make-to-stock (MTS) planning because it relies less on forecasts. It also helps overcome the challenge of long lead times associated with make-to-order (MTO) planning. DDMRP determines where in the supply chain to place strategic inventory buffers and how large these buffers should be.
The inventory buffers used in demand-driven material requirements planning are also referred to as “decoupling points.” This is because each stock buffer helps disconnect sequential lead times that otherwise accumulate and lengthen the delivery time to unacceptable levels. For example, if an inventory buffer is created between an intermediate, complex component and the assembly step that incorporates that component into the finished product, then the delivery time for the finished product is decoupled from the lead time for the complex component.
The reduced lead times offered by demand-driven material requirements planning help mitigate one of the critical drawbacks of make-to-order and other pull-type operations. Because sales orders trigger conventional MTO operations, production operations all occur between the time of the order and the time of delivery. By effectively moving some production operations to the period before the order is received, DDMRP reduces the time to delivery.
Demand-driven material requirements planning draws upon some aspects of MRP 1, combining them with elements from other production practices. Specifically, DDMRP employs a lean manufacturing pull method to limit the queues at each operation, and an emphasis on variability reduction from Six Sigma in manufacturing.
Related products: Opcenter Advanced Planning and Scheduling
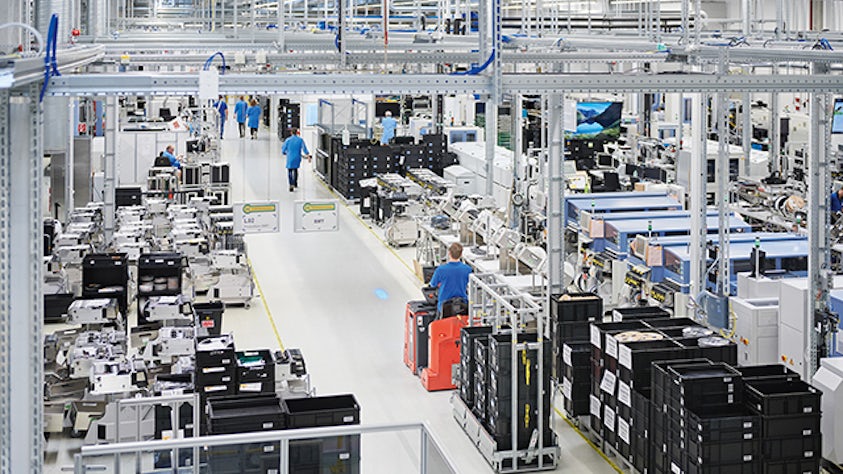