Defect management is a critical function within a quality management system (QMS): it enables manufacturers to track and trace deviations and corrective actions. Defect management also generates data that can be used by QMS, manufacturing execution system (MES) and manufacturing intelligence software to identify root causes and implement preventive measures that reduce or eliminate similar defects in the future.
Defect management relates to the software functions of both nonconformance management and corrective and preventive action (CAPA). A nonconformance is an unplanned event in the manufacturing process that deviates from a set standard or requirement. Such a quality event does not always result in a defect. The software identifies and documents of these quality events, and allows the manufacturer to apply standard risk criteria to assess and route events appropriately. It also enables enforcement of failure analysis, root cause identification, quarantine and final disposition.
CAPA software captures defects, nonconformances, and complaints. It then analyzes associated manufacturing problems, identifies root causes, determines corrective measures to be taken, and documents them. CAPA functionality extends beyond the manufacturing floor; it can interrogate the full spectrum of control points in a manufacturing operation, including design, production, documents, materials, facilities and equipment.
Related products: Opcenter Quality | Teamcenter Quality and Compliance Management
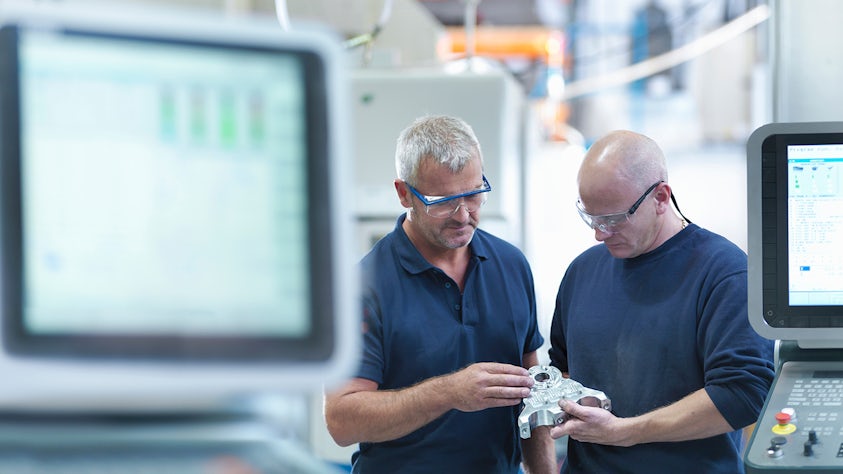