A CAPA system performs corrective and preventive action by analyzing a manufacturing problem, finding the root cause, correcting it, and documenting the correction. CAPA software captures various forms of complaints, defects, and non-conformances. The CAPA system provides a formal process to systematically investigate, analyze, and resolve identified issues. Streamlining the definition of measures to prevent reoccurrences of the problem, an effective CAPA system also reports results in a simple, intuitive user experience.
An advanced CAPA system resolves closed-loop issues and enables manufacturers to identify, analyze, and share critical product quality data across the enterprise. With an effective CAPA system, design, manufacturing and quality improvement teams can share the same views of the information they need to impact Six Sigma and Lean initiatives directly. CAPA software provides visibility into critical product quality characteristics, failures/non-conformances, and resolutions to these issues for smarter decisions across a global, extended enterprise.
Related products: Opcenter Quality | Teamcenter Quality and Compliance Management
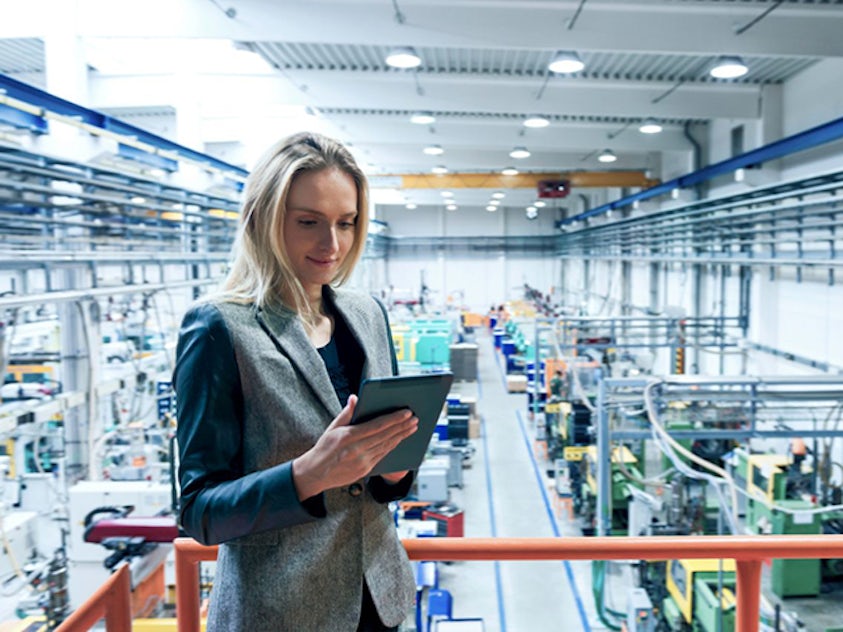