Aggregate production planning typically is applied to a 3- to 18-month period. Aggregate planning covers all production activities at a facility (or for large enterprises, across several facilities), not just individual production runs or manufacturing individual products. Because of this, aggregate production planning helps manufacturers optimize resource utilization despite significant variations in demand for individual products, which arise from changes in customer orders, supply chain dynamics, and other elements.
For manufacturers using digital systems in a manufacturing operations management (MOM) ecosystem, aggregate planning is a capability of an advanced planning and scheduling (APS) system. As a methodology, aggregate production planning can be performed using paper-based, spreadsheet or homegrown software solutions. However, the growing complexity of products, production operations, and supply chains has substantially increased the variety and volume of information that can be considered in aggregate planning. Therefore, manufacturers are trending toward greater employment of advanced planning and scheduling systems for their aggregate planning needs.
Aggregation planning aims to minimize operating costs by matching production demand with production capacity. An aggregate plan specifies what materials and other resources are needed and when they should be procured to minimize cost. The ideal aggregate planning outcome is maximizing a facility's productivity at the lowest possible cost to the manufacturer.
Related products: Opcenter Advanced Planning and Scheduling
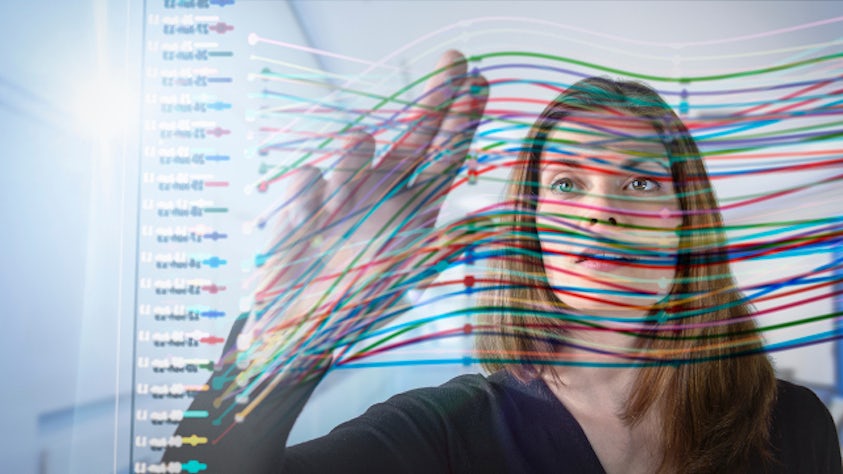