DDMRP wurde entwickelt, um Überbestände und Engpässe in der Lieferkette der Fertigung zu reduzieren. Der übergeordnete Zweck der bedarfsgesteuerten Materialbedarfsplanung zielt darauf ab, die Schwierigkeiten und Unzulänglichkeiten herkömmlicher Planungsansätze für moderne, komplexe Lieferketten zu überwinden.
DDMRP unterscheidet sich von der traditionellen Materialbedarfsplanung (MRP 1) und der Lagerfertigung (MTS), da sie sich weniger auf Prognosen stützt. Es hilft auch, die Herausforderung langer Vorlaufzeiten zu bewältigen, die mit der Einzelfertigungsplanung (MTO) verbunden sind. DDMRP legt fest, wo in der Lieferkette strategische Bestandspuffer platziert werden sollen und wie groß diese Puffer sein sollten.
Die Bestandspuffer, die in der bedarfsgesteuerten Materialbedarfsplanung verwendet werden, werden auch als "Entkopplungspunkte" bezeichnet. Dies liegt daran, dass jeder Lagerpuffer dazu beiträgt, sequenzielle Vorlaufzeiten zu entkoppeln, die sich sonst ansammeln, und die Lieferzeit auf ein inakzeptables Niveau zu verlängern. Wenn z. B. ein Bestandspuffer zwischen einer komplexen Zwischenkomponente und dem Montageschritt erstellt wird, der diese Komponente in das fertige Produkt integriert, wird die Lieferzeit für das fertige Produkt von der Vorlaufzeit für die komplexe Komponente entkoppelt.
Die verkürzten Vorlaufzeiten, die eine bedarfsgesteuerte Materialbedarfsplanung bietet, tragen dazu bei, einen der kritischen Nachteile von Einzelfertigung und anderen Pull-Verfahren zu mildern. Da Kundenaufträge konventionelle MTO-Vorgänge auslösen, finden alle Produktionsvorgänge zwischen dem Zeitpunkt des Auftrags und dem Zeitpunkt der Lieferung statt. Durch die effektive Verlagerung einiger Produktionsvorgänge in den Zeitraum vor dem Auftragseingang verkürzt DDMRP die Zeit bis zur Lieferung.
Die bedarfsgerechte Materialbedarfsplanung greift einige Aspekte der MRP 1 auf und kombiniert sie mit Elementen aus anderen Produktionspraktiken. Konkret verwendet DDMRP eine Lean-Manufacturing-Pull-Methode , um die Warteschlangen bei jedem Vorgang zu begrenzen, und legt den Schwerpunkt auf die Reduzierung der Variabilität durch Six Sigma in der Fertigung.
Verwandte Produkte: Opcenter Advanced Planning and Scheduling
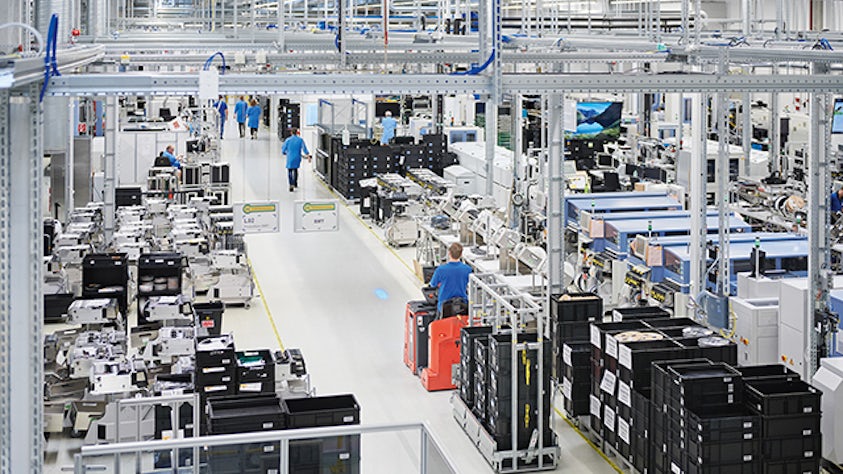